DANI | HOW WE WORK
The phases of the production cycle
Beamhouse
During the beamhouse phase, all the processes that prepare the leather for tanning are carried out: desalting, soaking, unhairing, liming in drums, mechanical scudding, trimming and splitting.
- Preliminary operations: the raw hides are cleaned and the subcutaneous fat recovered.
- Chemical operations: soaking, unhairing, liming
- Mechanical operations: fleshing, trimming, splitting.
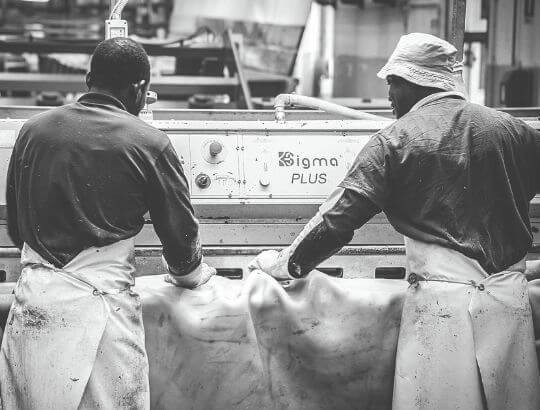
Tanning and retanning
Treating the leather in a drum with tanning agents followed by sammying, splitting and shaving. The tanned leather is called “wet blue” or, if tanned without using chrome, “wet white”. The retanning, dyeing and fatliquoring processes follow, which add colour, consistency and softness to the leather.
- Tanning: deliming, bating, pickling and tanning.
- Retanning mechanical preparatory operations: sammying, splitting, shaving
- Dyeing: retanning, dying, fatliquoring
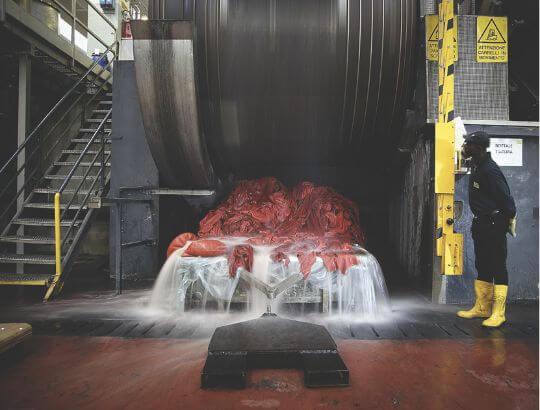
Drying and finishing
The first stage of drying is “sammying”, which allows the removal of excess water. Other drying operations follow (combined according to the characteristics of the article): vacuum drying, air drying and toggle drying. The dried leather is called “crust leather”. Various operations that make the leather soft and shiny alternate during the finishing phase: pigment spraying, protective resin spraying, wax spraying and staking. The finished leathers are selected one by one, measured, and then destined for different markets, from furnishing to footwear, clothing to leather goods.
- Drying: sammying, vacuum drying, air drying and toggle drying
- Refinishing processing: buffing, milling, spraying, pressing.
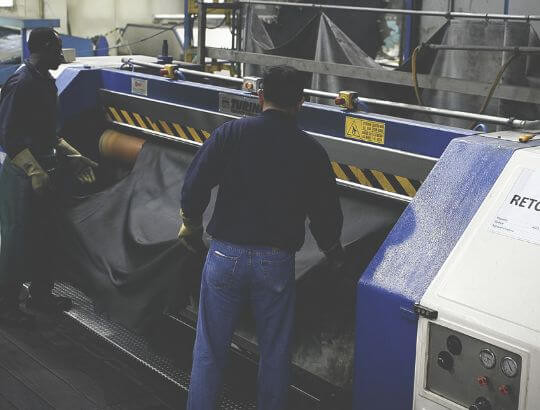
Final quality check
Before sending the leather to our clients, its organoleptic qualities are checked for the last time and it is tested in a laboratory, as agreed upon beforehand with our clients.
- Selection and sizing: the irregularities in each piece of leather are located and identified on the basis of fault catalogues supplied by each client.
- Laboratory: the Dani analysis laboratories, equipped with cutting-edge equipment and specialist technical staff, close the production cycle, guaranteeing quality and performance.
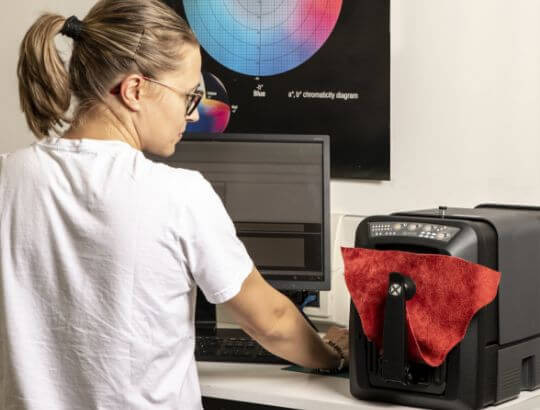
The checks to which we subject the leather are as follows:
- systematic checks on the performance requirements of each lot during all the production process phases;;
- written reports that give the results of the tests carried out;
- specific tests for the product destination sectors according to European and international standards; ;
- daily checks on the incoming chemical product requirements;
- research in process innovation arising from interaction and collaboration with departmental technicians.
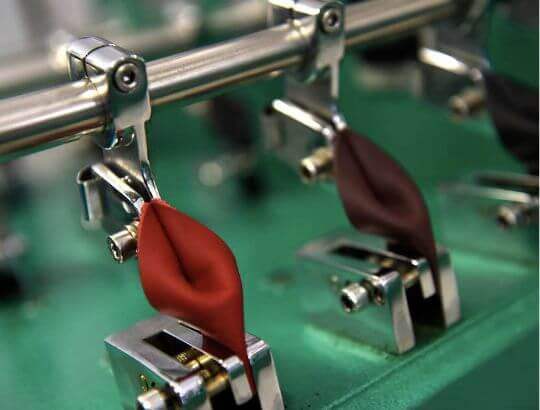
True Made in Italy
We are certified Leather from Italy – Full Cycle: the entire transformation of our leather, from the very first stages, takes place within the Veneto Leather District.
SEE OUR CERTIFICATIONS